Story by:
Bhushan Mhapralkar
Past the GST and e-way bill, touted as the most significant contributor to borderless travel and warehouse consolidation, the need for warehouse automation is on the rise in India as logistics companies and transporters look at further elevating the efficiency of transport. Warehouse automation in India in particular has been at a lower level, and the reason often cited is the easy availability of labour. This has worked in favour of the Indian logistics industry until now. Hereafter, the same may not prove to be as advantageous. The demand-supply situation is witnessing a drastic change. As consumer preferences change, and also expectations, automation to up transport efficiency is being touted as the best way forward. Especially to keep pace with the surging e-commerce trade and a potential threat from large organisations like Amazon.com. What makes it interesting is how transport efficiency could be elevated at the warehouse level, and at loading and unloading level.
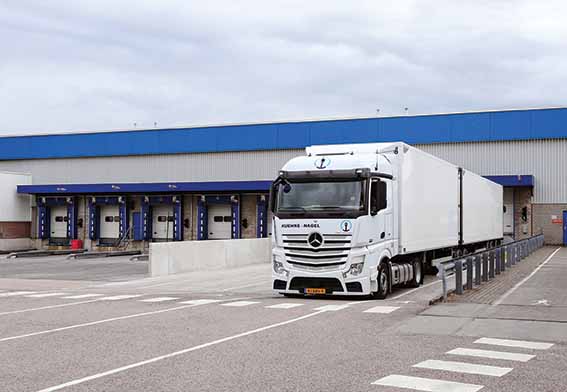
Loading and unloading of trucks in the most efficient manner is increasingly looked upon as the key element. In an environment where slowdown is eminent, it is the robot manufacturers that are getting closer to understanding this need of the logistics industry. They are also getting closer to solving it. If companies like Siemens AG and Honeywell International Inc. have built machines that can pull packages from the back of a tractor-trailer and place them on conveyor belts, the issue is more complex than it may seem. Even as the parcels whizz off for sorting, warehouse automation at the truck loading and unloading level is made complicated by the diverse nature of goods. With the presence of most global manufacturers and e-commerce players in India, the mediums of transport in India are beginning to change. Starting with a three-wheel cargo carrier to a heavy-duty truck, the change is visible in all the segments. Due to the complicated nature of goods and processes involved, making robots that can load trucks is proving to be complex. The good part is, clearing the hurdle is not as tough as it may seem.
A Tata Motors subsidiary, TAL Manufacturing Solutions, announced the launch of a TAL Brabo robot recently. It has been indigenously designed and developed to address the needs of micro, small, medium and large industries. Available in two variants of payloads of two-kgs and 10 kgs, the robot could complement human labour to perform high volume, repetitive, dangerous or time-consuming tasks. Successfully tested in over 50 work streams including lighting, aerospace, automotive, engineering, precision machining, software testing, electronics, plastics, education and logistics, the TAL Brabo is said to find takers at logistics companies in India as they look at automating various processes. If the automated guided vehicles (AGVs) deployed by e-commerce major Flipkart.com in the form of 100 robots to help sort packages at one of its delivery hubs on the outskirts of Bengaluru is an example, and how they are able to sort 4,500 packages in an hour, which is ten times more than a single human would be able to do manually in the same time, the loading and unloading trucks at warehouse bays, it is clear, will mark a big step forward. And, especially if its going to increase the system throughput by five times with minimal increase in infrastructure.
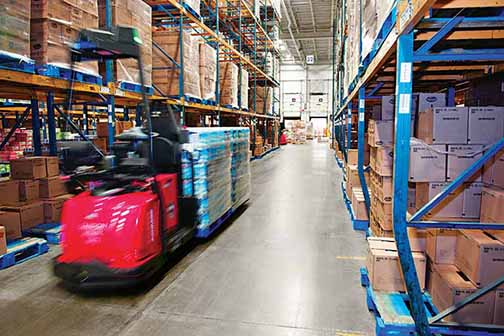
At a recent automation conference in Chicago, US, Siemens AG and Honeywell International Inc. displayed solutions that would address the issue of truck loading and unloading at a warehouse. The solutions pointed in the direction of how couriers are relying on automation to grapple with the rise in online shopping. They also pointed at the need to ensure good pressure on profit margins. If the automated unloaders took years to develop and still haven’t been perfected, reflecting the difficulty of working with an array of packages that are stacked differently from truck to truck, the automation solutions the two companies displayed also highlighted the need for space for machines in warehouses that could be already packed to the brim, or may have other equipment to handle some other tasks. The solution that Siemens displayed, requires modification of a truck’s trailer. Honeywell’s solution at the other end does away from the need to modifý the truck or the trailer. It isn’t as fast however as the Siemens solution.

Taking an hour to do what an average worker does in five hours, a robot developed by India’s largest warehouse robotics startup GreyOrange, is indicative of how warehouse automation is finding its way to India. It may not be advanced enough to load or unload a truck, it sure is helping online retailers and logistics firms to cut delivery time and costs. Operating from Gurugram, GreyOrange handles clients like Flipkart, Pepperfry, DTDC and Delhivery. Empowering its fleet of trucks to clock over 18000 kms a month, it is automation that is helping companies like Delhivery to up operational efficiency and quality, claimed an industry source. Such mileage was unheard of until now in India, he added. Generating a good deal of interest, the Honeywell apparatus on display at the recent automation conference in Chicago is worthy of being described as a behemoth on wheels. It has a bank of suction cups to grab packages stacked high. A portable conveyor catches or scoops them up from the trailer bed. Chances are that it would work best in a flat-floor trailer, and with the ability to unload as fast as a person could. This, minus the back pain and exhaustion.
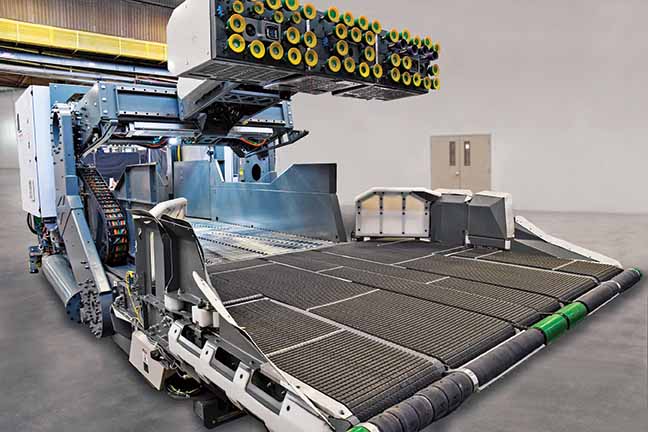
The basis for the Honeywell behemoth of an invention is the thinking that the job inside a trailer is miserable. Expressed Matt Vicks, Vice President, Product Development, Honeywell (Intelligrated Unit), on the sidelines of the display at Chicago, that getting people out of the trailer and on to the dock side to manage several of these machines is a huge task since it relates to employee satisfaction and retention. With abundant supply of labour in India, the Honeywell model of automation to up the efficiency of trucks in connection with the time spent at loading and unloading bays, may not prove to be the most attractive. Taking a different approach, Siemens has developed a rolling belt that could be permanently installed on the truck trailer’s floor with packages loaded on top. When the trailer is at the loading dock, a large machine is attached to the belt and packages are pulled in and sent to the sorting hub. Unloading a standard trailer takes 10 minutes, claimed a company source. He added that it would take approximately an hour for the same job to be done by one person.
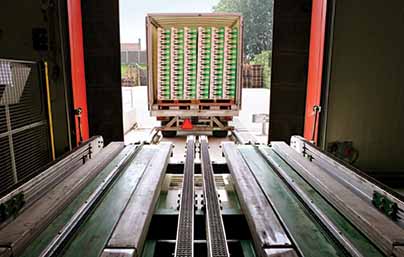
With fuel prices set to move up, any rise in transport efficiency will be greatly appreciated. And, especially from the view that trucks spend less time at the loading and unloading bays. The concept of trucks acting like aircrafts, and spending the least time idling, has already been floated by industry leaders like Vinod Sahay, CEO, Mahindra & Mahindra (Truck & Bus Division). This could well be the way forward for Indian truckers as they tackle various challenges and make every effort to stay afloat in the face of a slowing economy and falling demand. What makes it interesting regarding automation at the warehouse level, and concerning the loading and unloading of trucks, is how logistics companies like FedEx Corporation and UPS are experimenting. In markets like US, these companies are working towards automation in loading as well as unloading. They are doing so as the pace of online retail grows. Mentioned an industry source, that loading a trailer is tougher than unloading it from a three dimensional space point of view. He drew attention to the Dorabat, an entity that is supported by Chinese e-commerce titan Jack Ma.
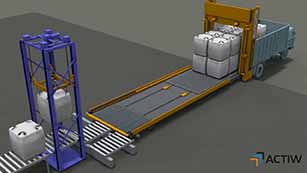
Dorabat is testing automated loading technology with two customers. The robots use artificial intelligence to display the capability to load 400 parcels an hour into a trailer. This amounts to roughly 60 per cent of the trailer’s capacity. Currently, it would be in line with what a person can do. The expectation is for the speed to go up by 50 per cent per hour. The expectation is to fill roughly 80 per cent of a truck’s capacity. With artificial intelligence by the side, this feat does not seem unachievable.