The recent spurt in fire accidents has brought the spotlight back on operator, occupant and pedestrian safety. Ashish Bhatia with Prateek Pardeshi checks on the push for manufacturing cost-effective EVs that are safe.
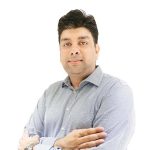
The reliability of Battery Electric Vehicles (BEVs) has taken a beating in the recent past with ad hoc fire incidents being reported across the countries. The hit was initially taken by two-wheeler EV startups serving the aggregate business model. They got the desired push early on as they rode the clean and green mobility wave. However, with the government forced to intervene with multiple such instances putting a question mark on safety, it compelled manufacturers to recall suspect product batches The draft EV policy emphasises on standardising EV battery packs. The focus has gone beyond manufacturing cost-effective EVs to building safe EVs. Pratik Kamdar, Co-Founder, Neuron Energy mentioned, “A lot of players are entering the industry without comprehensive knowledge of the batteries with regards to quality. The industry is still a fledgling one and the majority of dealers and customers are not educated or aware of the technology.” He advocated the need for a regulatory framework that ensures EV manufacturers and battery makers are held accountable for use of cells, Battery Management Systems (BMS), and compliance with regulations. “Even low-speed bikes need to be regulated by the government. EV manufacturers and battery makers should use fire-resistant grade battery materials along with superior BMS and best quality cells so these kinds of fire accidents can be avoided in the future,” he opined.
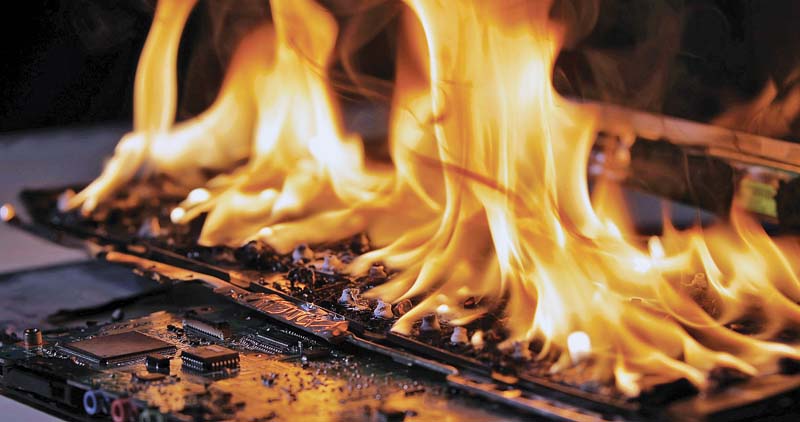
Forcing a rethink
There has been a spurt in vehicles catching fire across the board. Not just two-wheelers that are under greater scrutiny with some of the promising high-performance EVs failing to impress. In a noteworthy move, the government has instructed to halt the launch of new EVs in the segment until the incidents are probed to ascertain the cause of the fire. Fires have spread like wildfire to the more mature segments with relatively higher safety claims like the bus segment. With a history of select fire instances, it won’t be a bad idea either to revisit the safety checkpoints, especially for the operator, occupant and pedestrian safety that has a higher quantum of risk with these high capacity people movers.
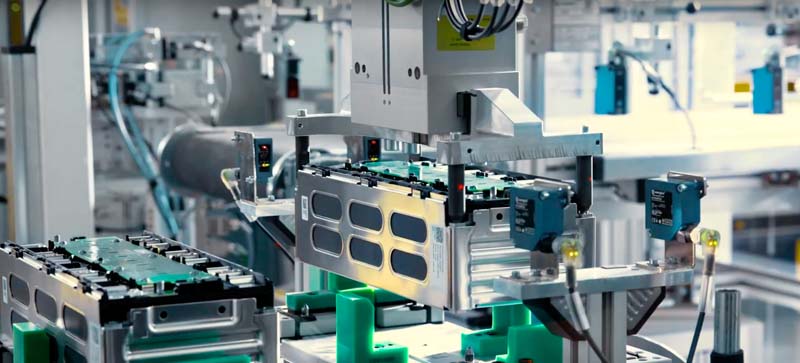
The situation demands attention, especially with the industry, thinking of alternative fuels and the government pushing for a gas-based economy. Alternatives include Compressed Natural Gas (CNG), Liquified Nitrogen Gas (LNG) and more recently the push for Hydrogen Fuel Cells and Electric Vehicles (FCEVs). An instance in 2019, comes to mind here. The BEST electric bus was reported to have left the Mulund bus depot one fine morning. A few minutes into the journey, the driver was alert enough to spot smoke fumes gushing out from the rear of this AC electric bus. Later on, a clarification was issued that the fire was owing to a case of overheating of the brake liners and not as a result of a spark or fire from the electric drivetrain. The bus, in this case, was from Olectra Greentech Ltd. and the company in its official statement confirmed that the smoke was due to the overheating of the brake shoe as a result of air leakage on the right-side booster and identified it as a common occurrence. Luckily, the bus is known to have been equipped with foam-based fire extinguishers with the Original Equipment Manufacturer (OEM) assuring all safety precautions and features on board the bus.
A Delhi Transport Corporation (DTC) CNG bus recently caught fire with 20 passengers on board in the South Delhi region of Mahipalpur. While it may have shifted the focus from commercial EVs, it must be credited with drawing attention to the safety aspect of alternative propulsion systems which is equally important. Notably, CNG penetration in the CV system is at an all-time high. In the aftermath of the unfortunate incident, OEM Tata Motors assured to fully cooperate with the investigation of the cause of the fire. In an official statement, the CV major reiterated its commitment to offering safe and high-quality vehicles for public transport. In another standalone incident, a luxury bus on the way to Kerala with 39 passengers on board is known to have caught fire. The firemen reportedly took over two hours to douse the fire made worse by plastic upholstery in the interiors. The extent of the fire was such that even the chassis of the vehicle is known to have been destroyed. In another instance, a TSRTC e-bus caught fire while charging. A short circuit was suspected to be the cause of the fire in the heavily damaged bus.
The fires are not limited to India. These are global phenomena. Paris recently suspended 149 e-buses from Bollore Groups’ Bluebus brand after two instances of fires. A Bluebus 5SE electric bus emitted thick smoke from battery packs located on the roof. Onlookers noticed a strong odour of plastic used in the bus. In South Korea, a Hyundai Motor Co. bus reportedly caught fire at the company headquarters with initial probes pointing at the battery pack.
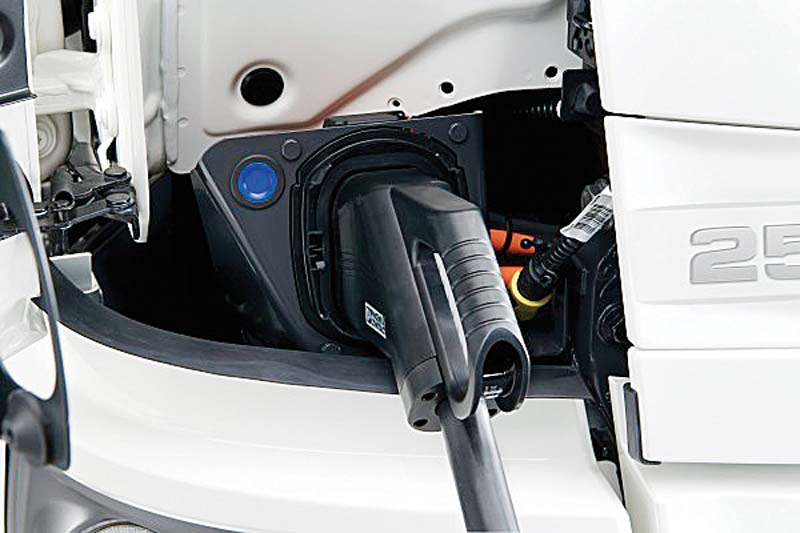
Naturally, the EV industry has faced a lot of heat! Kamdar blamed the substandard quality cells that are used by a majority of battery companies to manufacture battery packs with poorly installed BMS. Reacting to Niti Aayog member Shri V K Saraswat saying that “imported cells may not be suitable for Indian conditions”, Pankaj Sharma Co-Founder, Log9 Materials stated, “We welcome Shri V K Saraswat’s stance on indigenising Li-ion cells in all earnest and firmly believe this to be a pivotal point in the future discussions around India’s self-reliance in EV mobility. Developing cells in-house is critical for India’s self-reliance on Li-Ion cell technology. The majority of Li-Ion batteries brought into India are designed for different temperature and climatic conditions.” “Furthermore, India’s imports of Li-ion cells are low in comparison to worldwide demand; thus, leaving no incentive for the global Li-ion cell manufacturers to develop cell chemistries that are more suitable for Indian climatic conditions and application cases. Therefore, the only approach to producing cells for India is to develop chemistries suitable for Indian circumstances and manufacture them in India,” he opined. . Inline, the recent EV draft policy states that the standards approved or defined by BIS shall be implemented for the electric vehicle, battery safety requirements, degrees of protection (IP-code) of electrical equipment against foreign objects, and technical specification of cables and connectors, and traction battery safety requirements.
Kamdar also urged EV manufacturers to provide better spacing for batteries and to avoid the obsession with extreme compact sizes of batteries. “This can also be a cause of thermal runaway eventually leading to fire incidents. These instances can be avoided by reducing the under-seat storage by 30 per cent. Vibration pads need to be used to further ensure the stability of the battery pack. Thermal pads are required to be installed to ensure there is sufficient cooling mechanism,” he asserted. Besides measures on the supply-side, Kamdar also urged ensuring checks in places while transporting an EV from the manufacturer to the dealer. “The standard operating procedure should be followed while transporting an EV from the manufacturer to the dealer. Batteries should not be connected to vehicles during transportation. Batteries should be kept at a 30 per cent state of charge to avoid any risk of fire during transportation,” he added. Besides the above mentioned good practices, It is also imperative to store batteries in a cool and dry environment and avoid direct sunlight and water. Owners must take special care to quarterly service these batteries as fire instances do not occur in a day. “It takes 10-15 days before catching fire. If the batteries are being checked or serviced regularly such incidents can be avoided,” stressed Kamdar.
Compliance checks
It is learnt that the battery packs shall be tested and certified as per AIS 156 (2020) and AIS 038 Rev 2 (2020) standards for the safety of traction battery packs, as well as additional tests that may be prescribed for swappable batteries which are subject to multiple coupling/ de-coupling processes at the connectors. To ensure a high level of protection at the electrical interface, a robust infrastructure will be built that includes a rigorous testing protocol being adopted to avoid any dielectric breakdown, arc phenomenon, or any unwanted temperature rise at the electrical interface. BMS of the battery must be self-certified and open for testing to check its compatibility with various systems. This capability must meet safety requirements. Here, the compatible electric vehicles shall be tested as per relevant regulatory standards. For EVs with swappable battery functionality, vehicle OEMs shall be required to get ARAI approval for their vehicles to accept interoperable swappable batteries.
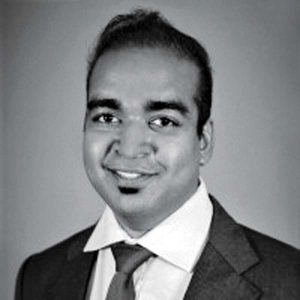
Localisation of battery
EVs are known to have a high acquisition cost. On the supply side, OEMs have justified this high initial acquisition cost with a low Total Cost of Ownership (TCO) over the vehicle lifecycle. The per kilometre charge consumption is said to outdo the running cost of Internal Combustion Engine (ICE) counterparts. The battery pack in an EV is the highest contributor to the customer acquisition cost. However, it is also true that globally, battery-pack costs are coming down. Cited Vishnu Rajeev – Head of Micelio Fund, “Lithium-ion battery value has come down drastically due to the course of massive investment which has gone under developing new technologies. Also with lithium-ion having a few shortcomings we are currently developing alternatives such as sodium-ion and other technologies.” In the short term though costs of battery cells have seen a 20 per cent spike blamed on the global surge in raw material prices including lithium. The prices are expected to remain higher for another year, it is believed. The Russia Ukraine war crisis has had a bearing too. The industry is also looking at means like recycling to enhance raw material availability.
In India, several supporting initiatives are promoting affordable EVs by way of localising battery packs for OEMs to realise economies of scale. From the Faster Adoption and Manufacturing of (Hybrid &) Electric Vehicles in India (FAME), I and II outlay, to the Production Linked Incentive (PLI) scheme for the National Programme on Advanced Chemistry Cell (ACC) Battery Storage (NPACC) to boost indigenous battery manufacturing capacity. State governments are also developing complementary policies to promote EV adoption according to Rajeev. He said, “Battery of EV accounts for almost 40 per cent of the total cost of the EV.” He drew attention to the traditional purchase pattern of EVs wherein “fixed” batteries are capable of only being charged using the external charging station while housed within the EV undergoing a transition with the advent of portable charging and swapping alternatives available to the customer.
Building economies of scale
There are no two ways of bringing the battery costs down. Localisation apart from the use of alternative and rear earth free metals is the most effective one that the industry has resorted to. India does not possess critical raw materials such as lithium, cobalt and nickel, which are used to make lithium-ion (Li-ion) battery cells. For example, Lithium-ion reserves are majorly found in two countries: China and Chile and recent trade volatilities have created a supply bottleneck, destabilising the supply and demand equation. Indian manufacturers continue to rely heavily on imports of battery cells from China, Japan, Korea, and Taiwan for assembly here. Most Indian bidders after the PLI scheme, are expected to commence localised manufacturing only by 2025. So, India’s import-driven strategy, for the domestic assembly of critical battery packs, will continue for a few more years giving a ray of hope for a quick turnaround.
Among promising initiatives, Reliance New Energy Ltd. acquired assets of Lithium Werks. The net transaction value of USD 61 million includes funding for the future growth strategy. Commenting on the Lithium Iron Phosphate (LFP), Mukesh Ambani, Chairman of Reliance Industries Ltd. is known to have said, “LFP is fast gaining as one of the leading cell chemistries due to its cobalt and nickel free batteries, low cost and longer life compared to NMC and other chemistries.” Lithium Werks happens to be one of the leading LFP cell manufacturing companies globally and has a vast patent portfolio and a management team said to introduce an immense value-add, especially in innovation across the LFP value chain.
In another example, Log9 Materials inaugurated a cell manufacturing plant in Bengaluru. It is expected to attain a 50MWh capacity in one year. It is positioned as one of the largest cell producing units in the whole of SouthEast Asia. The RapidX battery packs powered by InstaCharge technology are claimed to offer a 9X enhanced charging capability and better life. Omega Seiki Mobility (OSM) is known to have committed USD 250 bn for an electric three-wheeler manufacturing plant that also entails a battery pack supply chain. Suzuki Motor has committed to an investment of Yen 150 bn for EV projects including a battery plant in Gujarat. Tata Motors could benefit from subsidiary Tata Chemical’s interest in a battery manufacturing unit in Gujarat too.
Stressing the need to simulate fuel stations for ICE vehicles, deemed adequate, affordable, accessible, and reliable, he added that charging networks are required to attain a similar scale as a prerequisite for mass EV adoption. Efforts are underway in India to boost the availability of charging infrastructure with the recent tie-ups at public and private infrastructure and the emergence of special mobility zones in the country. Charging still takes a significantly longer time than refuelling an ICE but the customer has come to terms with overnight charging. Technology on the other hand has caught up to several claims of fast charge among capabilities like brake energy regeneration.
Battery swapping is an alternative which involves exchanging discharged batteries for charged ones and provides flexibility to charge them separately. This de-links charging and battery usage and keeps the vehicle in operational mode with negligible downtime. Battery swapping is generally used for smaller vehicles such as 2Ws and 3Ws and even buses using systems from companies like Sun Mobility. The smaller batteries are easier to swap, compared to four-wheelers. Battery swapping falls under the broader umbrella of Battery as a Service (BaaS) which involves users purchasing an EV without the battery. This is found to have been an effective alternative aimed at significantly lowering up front costs, and paying a regular subscription fee on a daily, weekly, and or monthly basis as deemed fit by the customer. BaaS is applicable for both fixed and removable batteries and is the channel for implementing the swapping solutions.
Also read, The country’s largest EV charging station opens in Gurugram