Story & Photos by:
Bhushan Mhapralkar
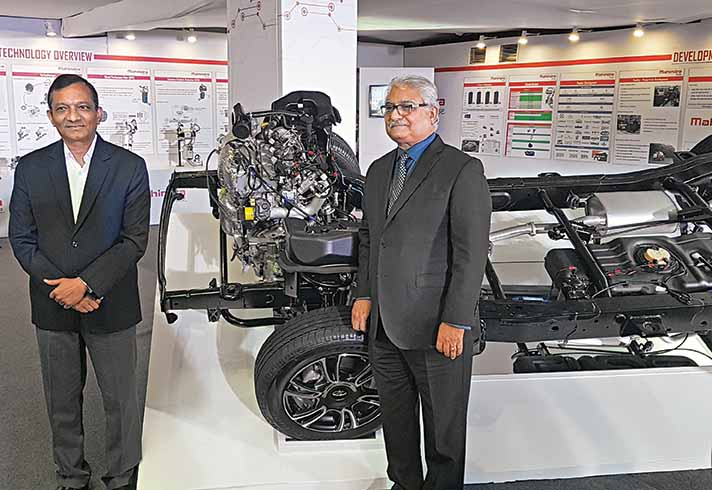
Succeeding in realising a scenario where local engineering and sourcing of BSVI technology was made possible in a short span of three and a half years at a much lower cost level in comparison to a scenario where technology and engineering would be imported at an exorbitant cost, Mahindra & Mahindra (M&M) has announced that it is ready for BSVI. It has announced that it is ready to go to the market with BSVI vehicles when the respective emission regulations come into force on April 01, 2020. Investing Rs.1000 crore in the exercise, the automaker put in place a strong team of 700 engineers to achieve the desired results. Of the firm belief that the move to BSVI emission regulation will be a non-event like the Y2K, Dr. Pawan Goenka, Managing Director, M&M, expressed that they have turned a challenge into an opportunity. “Our BSVI story has given a fillip to ‘Make in India’ even though the time frame of three and a half years to achieve the same called for much shedding of blood, sweat, and tears,” he mentioned. Announcing that the automotive business vertical of the group has gathered the same level of readiness at the M&HCV level too, Rajan Wadhera, President – Automotive Sector, M&M, said, “There will be a certain re-alignment of demand in-line with the costs involved in upgrading smaller diesel CVs.”
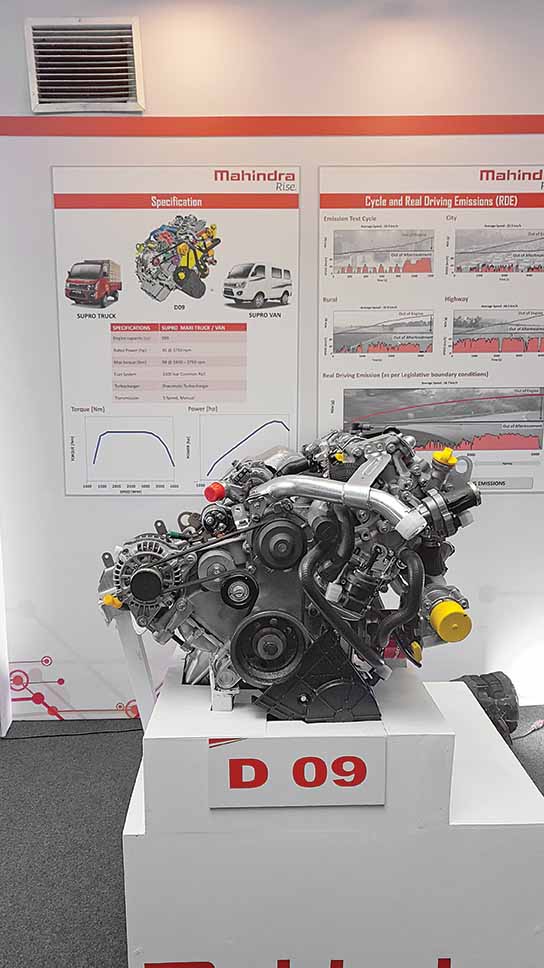
Upgrading all its automotive diesel engines starting with the Supro’s 909 cc two-cylinder turbodiesel motor and going up to the 7.2-litre motor that powers the Blazo HCV range as far as its CV product portfolio is concerned, M&M took an early lead in response to the BSVI announcement by the government. If the Supreme Court judgment to cease the sale of BSIV vehicles from April 01, 2020, added to the challenge, Dr. Goenka attributed the successful development of BSVI technology in part to the Indian auto industry’s ‘never say die’ spirit, and in part to the 700 people strong team that ventured out under the leadership of Rajan Velusamy (Head – Automotive Product Development), M&M, and Hemant Sikka (President & CPO, Power & Spares Business), M&M. He announced that they see no technical risk in getting a BSVI vehicle on the road. Planning the course and coordinating with suppliers and consultants, the BSVI team at M&M exceeded localisation targets and filed over 30 patents in the process.
Global reach, local touch
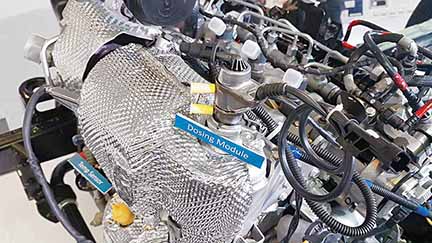
Working on a brief to achieve a competitive cost on the diesel portfolio, and to develop a portfolio of petrol engines that are globally competitive, the BSVI team achieved a cost of 0.5X against a target of 0.6X. Developing a portfolio of globally competitive BSVI petrol engines (some of them in collaboration with Ssangyong), the M&M team was able to execute the task with enough time to validate the aggregates and products. Said Dr. Goenka, “All the technological challenges were negated and products were engineered to offer more than just a shift from BSIV to BSVI.” He termed the cooperation between the company, and its suppliers and consultants, as the best he has ever seen. Adding state-of-the-art facilities in the process, including six test-bed dynos at the powertrain development facility, four mileage accumulation dynos, two portable emission systems, and various other equipment at Mahindra Research Valley (MRV), Chennai, the automaker is set to supply some of the gasoline (the turbo-GDI ones especially) engines to Ssangyong and Ford. Developing data acquisition and automation hardware as well as software as part of the accelerated durability test cycle for fleet validation, M&M will be ready with its first BSVI diesel and gasoline engine vehicle in the next three to four months.
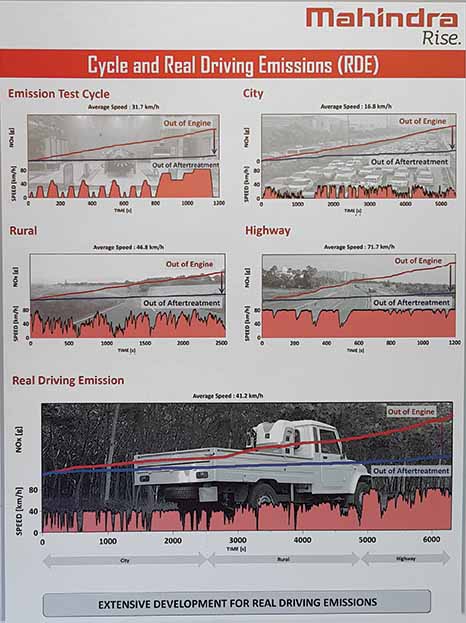
To launch the gasoline-engine vehicle sooner than the diesel one due to the unavailability of BSVI diesel fuel, the auto major is put a plan in place for 100 per cent production ramp down and ramp up across its many facilities. It has credited its suppliers (Bosch, AVL, and Delphi are key tech suppliers) for the success achieved in a short span of three and a half years. Averred Dr. Goenka, “The journey was exciting yet tiring for the engineers.” Providing a greater insight into the development process, Pankaj Sonalkar, Chief of Powertrain Engineering, M&M, stated that the BSVI team looked at pollutants, legislation, technologies, fuel upgradation and advanced engine management to conquer the BSVI challenge. With the diesel engine typically emitting particulates and NOx, and the gasoline engine typically emitting CO (the CO2 emission of a gasoline engine is 20 to 25 per cent higher) and Hydrocarbons (HC), the BSVI team at M&M worked on the engine as well as the exhaust gas aftertreatment.
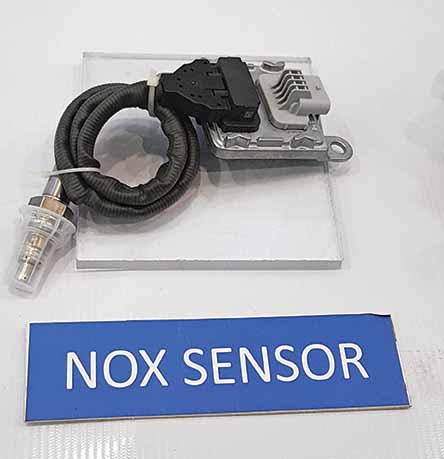
With the migration to BSVI from BSIV resulting in 68 per cent NOx reduction and 82 per cent particulates reduction in diesel, and 20 per cent reduction in CO and an eight-per cent HC reduction in gasoline, the team achieved a 30 per cent emission reduction at the engine level and a remaining 70 per cent at the exhaust level. The addition of a Diesel Particulate Filter (DPF) and the number of sensors in a BSVI diesel engine going up from eight to 18 would provide an insight on the complexities involved. What the BSVI team at M&M did, informed Sonalkar, was to indulge in extensive calibration. He pointed at the engine level changes pertaining to components like EGR, plunger pump, turbo, injector, throttle, ECU, dosing module, lambda sensor (the BSVI engine will use a linear unit over a binary unit), NOx sensor, differential pressure sensors, cDPF or sDPF, and DOC or an LNT unit. Taking into consideration each geographical condition, traffic condition, driver behaviour and issues like fuel adulteration, the BSVI team, worked out the optimal performance at the BSVI level.
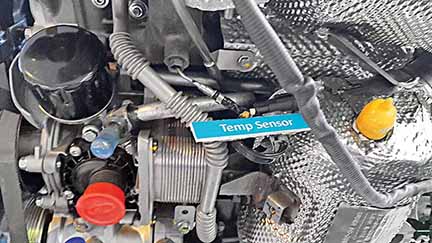
With every emission regulation upgrade known to result in efficiency and driving-performance loss, the team looked at every moving part in an engine. A 30 per cent friction reduction was achieved. The turbocharger was worked upon in cooperation with the vendor. To achieve higher thermal efficiency, it was integrated with the exhaust manifold. In the case of fuel injection system, challenges like higher injection pressures leading to higher noise were looked into. With the 30 per cent friction reduction resulting in a three-per cent fuel efficiency benefit, an amount of benchmarking against European export models was done. This provided a key to get the costs right. Deploying new tools, jigs and fixtures, and manufacturing dies, to ensure a smooth ramp down and ramp up across plants, M&M has come to have a BSVI portfolio that comprises of eight engines, 16 platforms and 13 variants on the diesel side. The BSVI technology that they possess includes a DPF as the key element with active and passive regeneration. Yielding 4,400 new components and a validation cycle of over 69 lakh kms, the automaker is ready with eight engines, 12 platforms and 12 variants on the gasoline side. Said Sonalkar, “Key technology suppliers, Bosch, AVL, and Delphi brought in their global experience.”
Efficiency, performance, and manufacture
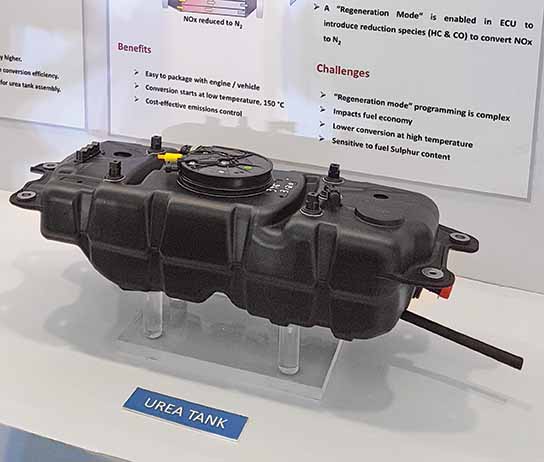
Making a strategic investment at MRV – the powertrain development centre especially, M&M has put out a strong team of over 100 people in the field for validation. The current fleet of 76 vehicles will soon be ramped up to 136 vehicles. This, according to Sonalkar, is complemented by 33,000 hours worth of cumulative test-bed validation across different cycles. Investing in seven centres across the country to tune its validation fleet, which is running on fuel provided by the Indian Oil Corporation, M&M has also set up a lab where parts are taken out from the mules after the day’s testing for a thorough checkup and analysis. Starting with much front-loading from the time the BSVI announcement was made by the government in February 2016 in close coordination with the suppliers, the automaker evaluated the most critical technologies. Revealed Senthur Pandian K, Associate Chief Engineer, Diesel Platform – PowerTrain Division, MRV, “By the time the final notification was issued, we were ready with the architecture definition for the engine and vehicle platforms.” “Post the approval of business case in March 2017, eight-engine platforms, 16 vehicles, and 38 vehicle variants were included,” he added.
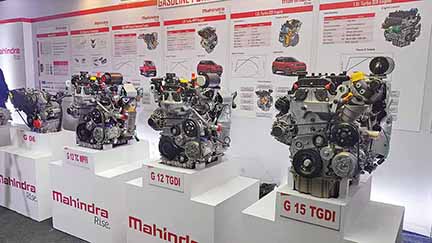
Entering design details, simulation and post-development followed by design release and rolling down of engines and vehicles, the BSVI team, informed Pandian, undertook the first major expedition in the summer of 2018. This was followed by a winter expedition in 2019. With the completely tooled engine and vehicle out for fleet validation, the stage of mature calibration is behind the team. Matters are at the certification level with few platforms in progress. The automaker is roughly seven months away from the start of the production. To work on CAFE and Stage-II development of BSVI, it is upgrading all its diesel engines in production currently. Successfully packaging key components like the urea (AdBlue) tank and DPF, M&M conducted rigorous reviews and closed workshops. It has also worked on real-driving emissions even though the legislation for the same is slated for 2020.
Future strategy
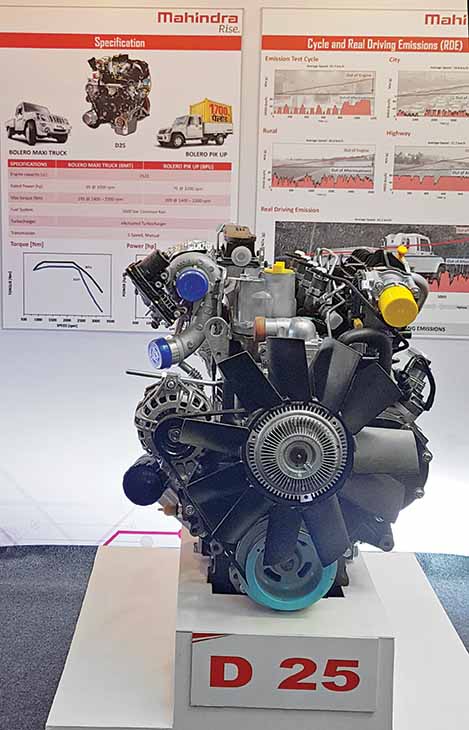
Upgrading its 115 hp, 1.5-litre four-cylinder turbo diesel engine that powers the XUV300 and Marazzo by retaining the same level of performance as a BSIV engine, M&M has deployed aftertreatment technologies that are specific to platforms in order to achieve the desired optimal performance for that particular platform. It has also upgraded the 140 hp 2.2-litre mHawk diesel engine that powers the Scorpio and XUV500. Mentioned Pandian, “The calibration of Bolero Pick Up and Maxi Truck engine proved to be challenging since the vehicles always run in a loaded condition.” “For real-world emission calibration especially, we took into consideration the top speed of the vehicles, which is limited to 80 kmph,” he explained. Stating that they are almost there in terms of legislation, Pandian said that almost all the developments have been completed. With 60 per cent of the validation work over at the diesel level, the automaker has developed an exclusive real-driving cycle for all vehicle platforms rather than wait till 2020. it is targeting the completion of the remaining 40 per cent validation work in the next few months.
With the Indian vehicles getting closer to European vehicles in terms of emissions, M&M’s BSVI journey has highlighted the fact that it would be impossible to meet CO2 reduction targets in the absence of diesel engines. Mentioned Dr. Goenka, “The absence of diesel engines would make it impossible to meet CO2 reduction targets.” He drew attention to the development of DPF technology in Europe when the EuroV regulations were introduced. Explained Pandian, “NOx reduction technology was developed to meet the EuroVI regulations in Europe.” Revealing that the boundary conditions for real-driving emission have already been legislated for different cycles in terms of altitude, temperature, maximum speed and duration of the test, Pandian stated, “The status of the test is yet to be decided however. Until 2020, it will continue to be at the monitoring stage.” Pointing at EGR, turbocharging and fuel-injection, the BSVI upgradation has led to 30 per cent NOx reduction at the engine level, he added. The tweaking of the fuel-injection system itself has led to 15 to 20 per cent of particulates reduction. The upgradation of the turbocharger has led to low-end drive-ability enhancement, the rise in hydraulic efficiency leading to an improvement in fuel efficiency.
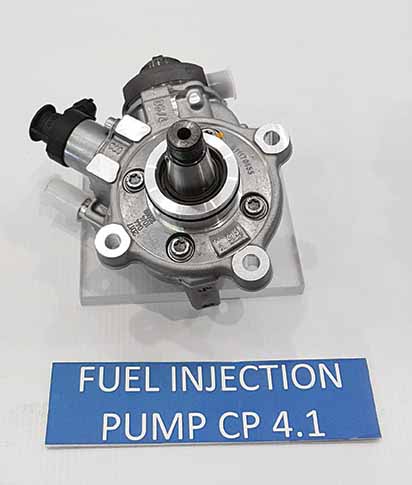
Deploying SCR technology in the interest of stability, the DPF on BSVI vehicles is engineered to work such that the ECU decides to automatically regenerate using some fuel when it gets full. The vehicles are said to have a switch on the dash, which activates regeneration of DPF after they are taken off the road for twenty minutes in the case of city use. Evaluating the lean NOX technology in terms of the challenges and opportunities it offers. M&M is looking at factors like cost, packaging, and reliability. It has done 95 per cent of the BSVI development in-house. Building competency spanning over a decade, and through export programmes, the automaker has worked on a good deal of standardisation for diesel. It has worked in close coordination with 125 vendors, of which 32 are technology vendors, according to Pandian. Set to profit from 99 per cent localisation of parts, M&M has designed and developed the gasoline engines ‘ground’ up. They have all the technology features that are in-line with the global benchmarks. Mentioned Prakash Rao Malathkar, Associate Chief Engineer – Gasoline & CNG Powertrain Projects, MRV, that the key factor separating petrol engines in terms of emissions is 25 per cent less NOx. He informed that a Non-Methane Hydro-Carbon (NMHC) component has been added in BSVI, which until now was unregulated. Retaining the base engine hardware, the aftertreatment system saw a drastic change at the petrol level.
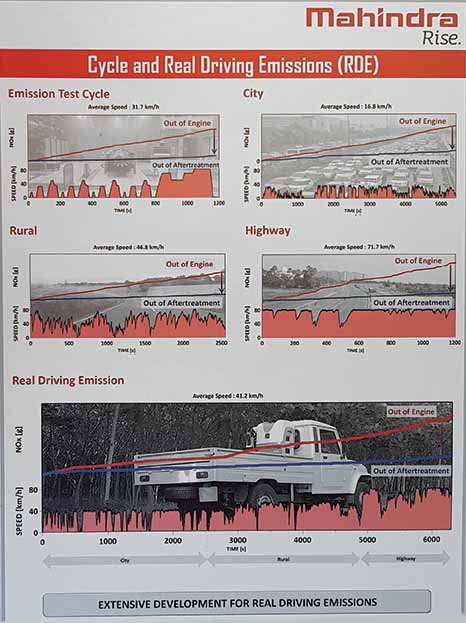
Leading to a 50 per cent increase in loading due to the use of a three-way catalyst, the development of BSVI gasoline engines led the auto maker to tackle CO2 emission in particular. With the CO2 emission in a petrol engine being typically 25 per cent higher than in a diesel engine, for CO2 reduction, 20 levels of technologies were looked at. Some of these included the use of a fully variable displacement oil pump to reduce parasitic losses and a decrease in CO2 emission by 2.5 to three-per cent. A variable valve train technology was roped in to enhance low-end torque and reduce pumping loses. It has led to a CO2 emission improvement of three-per cent. The integration of exhaust manifold with cylinder head led to higher power density and in-turn reduced the CO2 emission. The Turbo Gasoline Direct-Injection (TGDI) engines have a 250 and 350 bar pressure. The 350 bar pressure system will go into production by 2020, whereas the 250 bar pressure system is already in production, according to Malathkar. It has led to an improvement in fuel efficiency by three to four per cent, and a reduction in CO2 emission by seven to eight per cent. Displaying the 23 hp 625 cc BSVI single-cylinder all-aluminum engine with port injection for the Jeeto, M&M has hinted at a shift in focus to petrol for Jeeto. The same engine would be had in CNG guise.
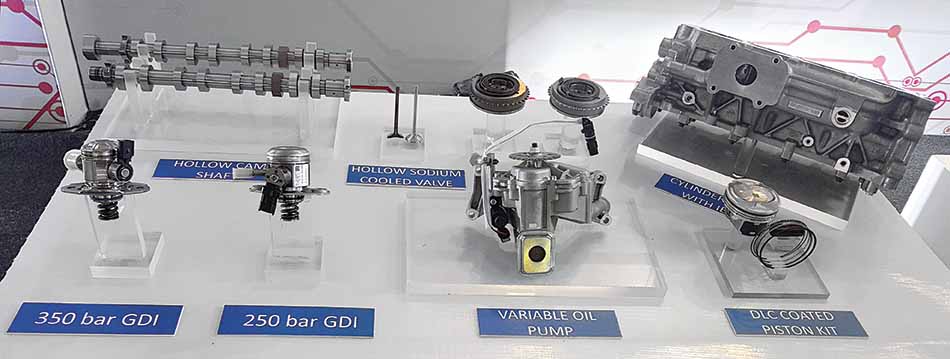
The 110 hp 1.2-litre turbo MPFI three-cylinder engine the automaker displayed will be BSVI ready in the next three to six months. The 130 hp 1.2-litre TGDI three-cylinder engine marks the (top) level of technology the company possesses as far as gasoline engines are concerned, and will be supplied to Ssangyong for Europe application early next year. This engine, to be also used by Ford for powering its platforms starting next year, packs the highest density in its class. It is available in BSVI as well as EuroVI version. The 163 hp 1.5-litre four-cylinder TGDI engine displayed will find use in M&M’s C-segment vehicles. A global engine, it was co-developed with Ssangyong. M&M is also working on yet another TGDI petrol engine that will be unveiled next year. It will further endorse its position as the petrol engine automaker. Stating that it is easy to migrate to BSVI with a 15 per cent drop, which would negatively affect drive-ability and fuel efficiency, Wadhera mentioned that they have done much work to ensure that such challenges are tackled to arrive at a much superior product. He revealed that the challenge of cost for BSVI smaller diesel engines is difficult to offset.
To educate its vehicle buyers about the need to maintain the AdBlue level in a dosing tank to avoid undesirable situations like the vehicle stalling or going into ‘limp’ mode’, Wadhera mentioned that operators henceforth will have to take into account the cost of fuel and AdBlue to work out the TCO. Stressing on the word ‘fluid economy’, he said that real-driving emissions will be a crucial factor in vehicle development in the future. Informing that the 1.2-litre KUV10 diesel engine will be discontinued for the BSVI development costs, Dr. Goenka said that their smaller platforms will contain gasoline and electric propulsion over diesel. He added that the Jeeto van will be discontinued for the high costs involved in its upgradation in terms of the safety norms. “The safety norms would make it essential that we fit it with airbags, which would simply make it unviable in terms of costs,” he informed.