Machines that move, haul and plough earth can capitalise on autonomous systems today via increased safety and productivity in the field and significant cost savings writes Ryan Gehm.

Autonomous operation for on-highway commercial vehicles has grabbed headlines and public attention, rightfully so since these haulers increasingly will share the roads with passenger vehicles. But there is a lot of interesting new core work occurring in the off-highway autonomy space as well, according to Brendan Chan, Chief Engineer of unmanned systems and active safety at Oshkosh Corp. “There’s the hub-to-hub stuff that everyone’s been talking about. There’s also a lot of geofences, low-speed applications where autonomy could be very useful and a very good value,” Chan said at the 2020 SAE COMVEC Digital Summit. Vehicles for yard manoeuvring is one such application. Mining and agriculture are two off-highway sectors where automated systems have proven effective and adoption is growing. Controlled environments and private property where regulations are less restrictive are driving factors. “The military is interested in autonomous systems as well, primarily as force multipliers and for occupant safety,” said Chan. “There is quite a lot of synergy in the autonomy space although the application may be different. It all boils down to the use case and the operational design domain,” he added.
Value proposition
What the mining sector is lacking, despite working on autonomy for the last 15 to 20 years, is that most of the autonomous systems are OEM-driven, closed and proprietary, said Prachi Vakharia, Head of alliances and strategic partnerships at Milpitas, California-based SafeAI. The mining industry can learn three things, in particular, from the passenger-vehicle side, Vakharia shared during the COMVEC session. First, working more closely with tier1 suppliers is vital. Building an ecosystem of partnerships is another beneficial practise, she said, referencing the Ford and Volkswagen collaboration to co-invest in Argo AI and its self-driving system. “The OEMs are working together in this; they’re not all building their own autonomy solutions independent of each other,” she said. The third point is the robust startup ecosystem that exists with on-highway CVs and passenger vehicles. “These companies have made so many advances in autonomy,” Vakharia said. “They’re using the best in Artificial Intelligence (AI) and machine learning. They are using and creating some of the best hardware that’s possible,” she cited.
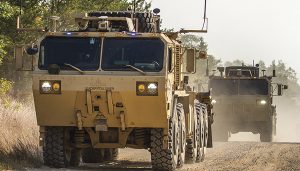
SafeAI is trying to change this model by supplying an open, interoperable autonomous software platform with “industry-specific AI” that can be retrofitted to existing mining and construction equipment. “Only three per cent of mobile equipment at any mine today is autonomous,” Vakharia said. “So that tells you there’s a huge gap to be filled.” Taking its own advice, SafeAI announced on October 22 a partnership with Japanese construction company Obayashi Corp. to operate an autonomous Caterpillar 725 articulated dump truck on a Silicon Valley test site beginning November 2020. The Cat 725 will demonstrate load-haul-dump cycles. The pilot program is a precursor to the companies creating autonomous construction sites around the world.
Still, mining will see autonomy in production “much sooner” than on-highway applications and even before construction, according to Vakharia. “The operational design domain is much simpler. But the other thing is the value proposition is simply much stronger, especially for mines,” she said. Fleets can benefit from shorter cycle times and the need for fewer vehicles. Vakharia cited data showing that haul-truck productivity can increase by about 21 per cent due to increased utilisation. Fuel consumption can be lowered by six per cent, and tyre wear improved by 7.5 per cent. Autonomous-haul trucks can have a 49 per cent after-tax internal rate of return including labour savings. And of course, improved safety is part of the equation. “There are about 200,000 safety incidents that are reported in the U.S. at mines, and they want to dramatically reduce this number,” she said. “So, you can move people out of hazardous conditions and also add value to their jobs by giving them more high-skill jobs, where they’re managing machines and doing less-repetitive tasks,” she opined.
Mixed Ecosystem
Strategic partnerships are important to advance autonomy in agriculture as well. A pairing revealed in mid-October has Kubota and California-based Nvidia teaming to develop fully automated and unmanned agricultural machinery. Kubota tractors will be equipped with Nvidia’s end-to-end AI platform, including graphics processing units and artificial intelligence coupled with cameras. “This will contribute to the sustainability of Japanese agriculture, where the agricultural population continues to decline,” Kubota stated in a LinkedIn post. This partnership follows the unveiling earlier this year of Kubota’s “dream tractor.” The X Tractor electric crawler concept obtains and evaluates environmental data such as terrain, weather conditions and growth rates to choose the appropriate operation. The data can be shared automatically with other machines at the site for more efficient operation.
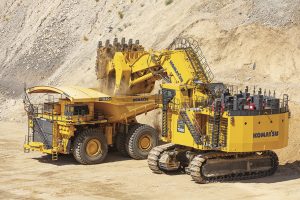
Agricultural machinery is a major focus of CNH Industrial’s autonomous development activities as well. Brett McClelland, Product Manager focused on autonomy and precision agriculture at CNH industrial, stated that much discussion gets focused around the final embodiment of autonomy. “However, one of the bigger challenges that doesn’t get as much airtime in our off-road space is this progression towards autonomy,” he said, adding that there are many meaningful operator-assist steps along the way to SAE Level 5 autonomy.
“What we’re finding is that you have to push subsystem automation so far and make these machines so capable of monitoring their own health, their own performance, that along the way you can actually deliver these back to the customers as simplifications,” McClelland explained at the COMVEC Digital Summit. “If you can take a system where today it requires multiple inputs from the operator, either through a touchscreen or pedals or switches, and you can turn that into something like a one-button click to go, not only have you prepared your machine and your subsystems for autonomy, you’ve also streamlined and improved the experience for the customer,” he added.
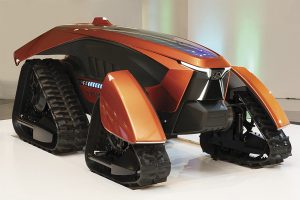
Another challenge is managing the “mixed ecosystem” that likely will persist for decades before entire fleets convert to full autonomy. Manned and unmanned vehicles will operate in the same fields often in proximity, so companies must consider how to make this environment manageable for farmers.
“There’s a combination of tools that we provide customers today to manage these manned vehicles, typically a combination of in-cab technology and then cloud or web technology,” he explained. “But in this future paradigm, you have to provide not only controls and visualise data for that machine, you have to visualise it for the whole team. And then outside of the field of operation, today we traditionally provide cloud telemetry type solutions. “Ultimately, those have to evolve as well,” McClelland noted. “So, I expect this to drive a lot of change in how we provide some of these services in the near future,” he opined. CV
…………………………………………………
Courtesy: Mobility Engineering
Also, read SIAM’s virtual press conference for quarterly data