One of the largest tractor plant is in Hoshiyarpur, Punjab. Sumesh Soman visited the Sonalika Tractors shopfloor to get a sense of the new manufacturing advancements and operational peaks
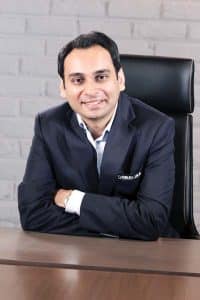
Sonalika brand of International Tractors Ltd. (ITL) in the month of October 2022 clocked a delivery of 20,000 tractors which was its highest-ever wholesale dispatch. It also marked 16 per cent sales growth on a Y-O-Y basis compared to a seven per cent growth in Total Industry Volume (TIV) for the same period. Raman Mittal, Joint Managing Director, Sonalika Group, said, “We feel very proud to have attained yet another milestone last October with our ever-highest deliveries of 20,000 that helped us register a 16 per cent billing growth more than double the established seven per cent industry growth.” “Such a performance is extraordinary for us as we planned for a target and we achieved it 100 per cent. Every team member across verticals put their best foot forward for an extraordinary drive until the very last day,” he expressed. The plant that the company has in Hoshiyarpur is instrumental in achieving such benchmarks on a recurring basis.
At the 125-acre plant, the shopfloor account for 14 acres alone. The visit to the shopfloor helped ascertained the scale of operations. It is capable of producing 750 tractors on a daily basis. That translates to pushing out one tractor every two minutes in a three-shift cycle if one were to take into consideration an eight-hour production shift. That amounts to 22,500 tractors monthly and an estimated 2.7-3 lakh tractors annually. Inaugurated in 2017 at the hands of Punjab Chief Minister Capt. Amarinder Singh, Mittal drew attention to the scale of operations and has brought in much cheer in the crucial, last festive season. “Our strategies and business realignment initiatives have resulted in a magnificent festive season for us in FY23. We shall continue to launch new exciting products that will exponentially increase farmer productivity and income for years to come.”
The manufacturing facility produces key components like the crankcase, transmission case, clutch housing, brake housing, and axle housings to name a few. The machinery used to test and build these components are again a healthy mix of both domestic and imported equipment from companies like Mazak, DMG Mori, BFW Machines, and Jyoti. Sonalika ITL, according to Mittal, enjoys a 25 per cent export market share which translates to every fourth tractor exported being a Sonalika. The company recently recorded a sale of one lakh tractors in a time span of eight months helping it set an internal best record. This includes a vivid 11.2 per cent YTD growth recorded during Apr-Nov’22 higher than the industry average of 8.8 per cent on a YTD basis. Not a one-off, Sonalika ITL has been clocking one lakh tractor sales for the last six years now, from FY2018-23. Mittal attributed the feat and consistency to a deep market understanding and an impeccable farmer connection. “From aiming for 50,000 tractor sales at one time to clocking one lakh tractor sales consistently for the last six years, it is a testimony of us delivering on our promises,” he asserted.
Raising the bar
In September 2022, the plant attained a benchmark of manufacturing 15,563 tractors which chalked another milestone in the production history of the facility. The state-of-the-art, largest tractor manufacturing plant has high levels of automation. It is integrated with robotic welding, laser cutting, gear shop and paint shop terminals that work in tandem to feed the main assembly line. The tyres and pumps are the only ancillary components known to be out sourced by the company. Everything else is claimed to be built under one roof and that is quite the feat! The company procures its tyres from tyre OEMs like MRF, BKT and Goodyear to name a few.
It’s the in-house facilities that allow for this distinction. For instance, the transmission line at the facility is capable of pushing out 220 transmissions in one shift, and there are three shifts in a routine day. This can be tweaked according to the supply and demand dynamics of the market. The components terminal of the facility is capable of pushing out 420 fenders in the eight-hour shift. There is a segregated facility that is responsible for manufacturing 250 numbers of plastic components and these parts have their separate gauges to perform independent quality checks. The paint shop at the plant also benefits from automation. Robots are tasked with the paint job on the chassis; it optimises paint consumption while also reaching all the concealed crevasses on the chassis. The robot scans the model code on the chassis and detects the path of its travel while it sprays the paint. These robots are also used to load parts on machines in a bid to reduce manual intervention and increase Turn Around Time (TAT).
Additionally, fasteners of all critical joints are torqued through multi- spindle DC tools and in turn generate the data on a common server for analysis and recording. All fluid dispensing units are centrally connected and dispense metered quantities of fluid based on the model code of tractors sensed by them. The tractors are equipped with the ‘Skysmart’ system powered by the ‘Sonalika Tiger’ application for real-time location tracking of the tractor in the field and for promptly supporting farmers in their service needs.
Checks and balances
The quality gates at the facility generate an ‘e-travel card’ that serves as a digital dashboard for the tractor and bears crucial metadata. This ‘e-travel card’ is meant to be referred to by the field team for regular updates on the production cycle. These digital gates are further connected to monitors on the assembly line. Defects captured during any of the inspection stages or PDI are promptly relayed to these screens and tag the personnel directly accountable for instant feedback. The system is designed to generate data for defect analysis and corrective actions. It is made possible by digitally assigning and engraving a chassis number that also carries the model code of that variant along with a bar code for ready reference across the multiple assembly stages including and not limited to engine, transmission, sheet metal parts, fuel tank, rear and front tyre assembly, radiator, steering, hydraulics, seat, headlights, and the wiring harnesses.
All the ‘in-process’ and final product test rigs, conveyors and measuring equipment generate data which can be viewed on a real-time basis, analysed and archived for future reference. Scanners installed on all the line stages make it possible to scan the model code and display the part codes among other metadata, key to fitting the components on the particular line stage for a particular variant. Back flushing (confirmation of production and consumption of related parts) is digitally done at different stages by all the production units. In the same vein as the digital footprint across the plant, a digital manufacturing system at the plant links the skill matrix of the workforce to a biometrics attendance system. This Sonalika Production System (SPS) automatically deputes workers on various line stages based on their skills at the beginning of the shifts. It is further linked to multiple quality gates where the captured defects are directly displayed to the concerned person responsible. These quality gates detect defects and also confirm adherence to specifications as mandated by the R&D unit.
Of the opinion that the farmers are slowly but steadily, coming around the wave of farm mechanisation as the right way forward if one were to attain higher productivity and assure oneself of a consistent income in the existing agricultural ecosystem. Mittal quipped that product upgrades today were no longer limited to the festive and it has been possible to considerably decrease the product replacement cycle as well. “We are thankful to all our customers for their trust and will make sure that we keep delivering on our commitments for farmers across the world,” he stated.
The manufacturing prowess at Sonalika ITL is backed by a strong R&D unit. It has allowed the company to offer a wide range of tractors, ranging from 20-120hp with over 70 variants in the mix. The R&D at the integrated tractor facility is manned by a 300-member staff that conducts studies and helps in developing products that are both affordable and durable according to Mittal. With over 1.4 million customers and a strong footprint in over 120 countries across the globe, Sonalika is banking on its products: Tiger, Sikander, Mahabali, Chhatrapati, Maharaja and Smart Harvester to name a few. The company also has the ‘Tiger Electric’ at a price tag of rupees six lakh to help it stand out and meet the needs of evolution. To introduce a layer of transparency, Mittal pointed at the publicly available price range of its entire portfolio in an “unparalleled” move. “Farmers today are progressive and remain well informed, thanks to the rapidly growing digitalisation. Prices play a crucial role in simplifying the decision matrix for a tractor purchase but for ages, transparency on prices have remained one of the few challenges in the tractor
industry.”
Also read,