With bus body code regulations in place, JCBL is looking at setting the pace.
Story by:
Anirudh Raheja
Chandigarh-based JCBL was established in 1989, with a mission to design and manufacture high quality buses and load carriers that are stylish, well engineered, and have high standards of reliability. Serving the commercial vehicle industry for the last 25 years, the company has built luxury buses, integral coaches, school buses, special application vans, medical vans, motor homes, armoured vehicles, agricultural implements, tippers and tip-trailers, cargo carriers, refrigerated vans, and heavy haulage tippers. Specialising in the manufacture of bus bodies especially, JCBL, with the AIS (052) revised bus body code in place, is looking at setting the pace. From January 01, 2017, buses, under the bus body code, will need to be classified into specific types as per the guidelines of the Central Motor Vehicle Rule (CMVR). They will need to be built as per the set specifications, and should have the necessary approvals from the respective transport authority. According to Rishi Aggarwal, Managing Director, JCBL Ltd., with AIS 052 bus body code in place, the government is stressing upon improved safety in CVs. “Looking at the rising pollution levels, and the demand for safety and comfort in India, the implementation of stringent norms like the bus body code and BSIV emission norms is the need of the hour,” he adds. Sanjeev Babbar, Chief Operating Officer, JCBL Ltd., opines, “The bus body code will be implemented in two parts. Broad specifications will need to be met in terms of dimensions. In 2018, the second phase of bus body code will be implemented, and will call for specific structural rigidity and structure FEA requirements.” “Specifications will also call for window retention, seat testing, anchorage, headlight and windshield swipe tests,” he adds.
OEM support
Over the 25 years of its journey, JCBL has come to work closely with almost all the CV OEMs in India. It has thus experienced, first hand, the industry ups and downs. Witness to the current turbulent times with pan-India BSIV emission regulations to be enforced on April 01, 2017, followed the announcement of GST in July, JCBL is confident of achieving strong growth despite the challenges. With the sleeper coach code expected to be announced soon, the company, despite the near future of the CV industry looking more or less unpredictable, continues to be bullish about growth. Undeterred by the low double digit growth registered last year by the bus industry, JCBL is optimistic about a bright future. Says Agarwal, “JCBL has been a strong support partner for Ashok Leyland and SML Isuzu for their pan-India bus business for many years.” “Close to 50 per cent of the business carried out by JCBL comes from these two OEMs,” he adds. Out of its four manufacturing lines, JCBL has developed two lines for Ashok Leyland and SML Isuzu each. The company would build school and staff buses for both these OEMs. The third line, JCBL has specifically developed for Ashok Leyland ambulances. The fourth line caters to private businesses, including those that demand bullet proof and armoured vehicles.
JCBL body built 170 mini buses for SML Isuzu last year as part of an order received from the Chandigarh Transport Undertaking. JCBL recently completed an order of over 170 life-saving ambulances to Ashok Leyland. These ambulances were supplied by Ashok Leyland to African markets. The company has bagged an order for 1,000 ambulances from an OEM. These would be supplied to defence forces, and are specifically tailored for defence applications. To reduce the time it takes to build a bus body, JCBL has developed a mechanism where a fully fabricated body is ready. This is being practiced for SML Isuzu. A fully fabricated body is married to the bus chassis before the paint process. “Much time is saved,” avers Babbar. “Not only does this cut down the manufacturing time to seven days, down from 20 days taken for an LCV, it also allows us to work on lean inventories. Two more days of body building can be reduced if the body-chassis marriage can take place after the body shell is painted,” he adds.
Container bodies
JCBL supplies truck container bodies measuring between 22 ft. and 40 ft. to Ashok Leyland ICVs and MCVs that range between 10 and 16-tonnes. JCBL is executing an order of 500 32 ft. containers for Ashok Leyland medium and heavy-duty trucks against an order for 1200 trucks placed by logistics start-up Rivigo. With the truck body code on its way, load body trucks, LCVs especially, are already being built by OEMs. Opines Babbar, “Cargo transportation hereafter will be safer. It will be done in a box. The market would thus graduate to container transportation model of business.” “The progress in truck code has already started with the cabin _ with AC fitted cabins. For load bodies too there will be compliance necessary. OEMs are working with various body manufacturers on this,” states Babbar. Strategically located to cater to the needs of SML Isuzu plant at Ropar, and Ashok Leyland plant at Pantnagar, JCBL is increasingly looked upon as an application builder that can address the requirements of OEMs as far as the North Indian markets are concerned. “We are working with Mahindra for the design and development of their new platforms,” reveals Babbar. He adds, “For Tata Motors, we are doing Light Armoured Troop Carriers (LATC) and special application vehicles related to defence applications like ambulances and bomb disposal squad vans.” JCBL has approvals from Ashok Leyland and SML Isuzu for their LCVs and ICVs. This, says Babbar, will be a significant growth area for JCBL in the coming times. JCBL is also gearing up for medium-duty vehicles in the next quarter. The company recently supplied two election campaigning vans to Samajvadi Party leader Akhilesh Yadav apart from a few other chief ministers. These vehicles highlight the company’s abilities to build motor homes, mobile offices, and bullet proof vehicles.
Adapting to changes
The ability to adapt to market changes has seen JCBL in good stead. JCBL has honed itself to quickly respond to changes as well as anticipate them. Says Babbar, “The peak season for bus sales starts from January and extends all the way to July. It is during this period that JCBL has to raise production to as much as 600 buses per month. The paint shop has to be run in three shifts, and the plant has to operate in extended shifts. The rest of the year witnesses drop in sales. We have to quickly adapt to such market changes, and more.” A labour intensive business according to Babbar, JCBL has to do much planning. It has to anticipate. “Optimisation of capacity and maintenance of business cycle is necessary. One achieves good results in an year if an order for additional 150 to 200 units per month is bagged,” avers Babbar. Adhering to yearly targets is necessary, and beyond that, that is where the growth lies. In case of an overlap, old orders can affect the performance of the company in the next season. To drive growth, clearing old orders expeditiously, if any, and concentrating on current business is a challenge that the team under Babbar is managing well.
Gearing up for the future
The last seven months have been a busy period for JCBL. The company facilities are being upgraded to comply with the AIS 052 standards. “Whether it is a bus for an OEM, or for the private sector, approvals are necessary. This makes it necessary to have a common base structure and platform. It enables faster approvals as tests are necessary even when you integrate body with the chassis,” explains Babbar. Once the design structure for a particular payload capacity is ready, structural FEA clearance becomes necessary. Clearance is also necessary for components and aggregates like seats, anchorage, window retention, placement of headlights, windshield wipers, etc. “Any change in aesthetics is fine; any change in the structural design needs approval,” mentions Babbar. According to him, once the chassis is up to a specific operation, the body has to be designed as per the requirement. It has to match the placement of the engine (rear or front), floor height, air-conditioner, etc. The nature of application has be taken into consideration as well. “With the bus body code in place, road side bus body building will be redundant. This will lead to an increase in the business of established players,” opines Babbar.
An estimated 40,000 chassis are sold in a year. This is set to change. With the emergence of various codes, stress on fully built vehicles is expected to rise. The same is already happening, says Babbar. Manufacturers are under pressure to achieve good numbers. “Those players that do 35 to 40 bus bodies per month are pumping investments despite demonetisation to comply with the new standards. This is not easy. The good part is, safety will be elevated,” avers Agarwal. JCBL has a capacity to manufacture 5000 buses and 8000 load bodies per year out of its two plants. A mid-size AC bus takes up to 20 days to manufacture. A medium-duty commercial vehicle takes up to 35 days to build. JCBL has invested in a full fledged R&D centre at its Lalru plant. It spends up to four per cent of its annual revenues on research and development. Says Babbar, “It is not that every time we look at numbers only. We use revenues by changing the product mix, or by increasing the unit sales, or by doing both. There has to be an optimum value addition that one is able to generate at the end of the day.”
Comfortable ride
To keep up with the changing needs of the market, JCBL has tied up with Eberspacher Sutrak and Spheros Motherson for the supply of bus ACs. Drawing attention to the rising demand for AC buses, Babbar says, “Aggregates like ACs, roof hatches, air curtains, and electronic gadgets are playing an increasingly important role in the building of bus bodies. Demand for comfort is rising. It is to address this demand that we have tied up with respective suppliers.” Aware of the growing electronic content in CVs, Babbar points at the rising use of LED lighting systems, including LED head lamps. He expresses, “OEMs are already working towards the approval of LED lights in bus body manufacture. Cost is not a hindrance. To get into an arrangement with manufacturers of such specialised components is important.” Emphasising upon his company offering support to their customers, Babbar opines that an arrangement with manufacturers of such specialised components will help us further. Their channel could be leveraged to provide service to our customers, he adds. The idea is to provide a comfortable ride to the customers as well as those who ride JCBL built buses.
Of the opinion that rear-engine buses are growing in numbers, Babbar avers that by addressing the changing needs of the market, the opportunities to grow for companies like JCBL will only increase. He points at the sleeper bus specification draft, and opines that ‘legal’ sleeper coaches are not far. “As night-travel by buses increases, it is becoming increasingly necessary for OEMs to look at a capable partner that will help them to tap the trend. Quantum jump in technology is necessary for a better tomorrow. There will be challenges, but the need to upgrade will be there. Consider the example of deployment of CNG buses in Delhi,” mentions Babbar. In its effort to support its clients, JCBL has opened offices and service centres at Delhi, Hyderabad, Chennai and Mumbai. The company is also closely working with OEMs; it is allowing access to their dealer network. Apart from local teams that provide service support, JCBL has mobile teams at the plant, which help in the delivery of orders as well.
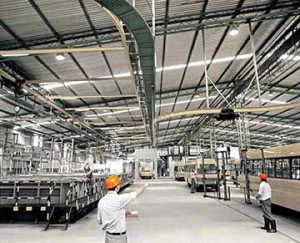
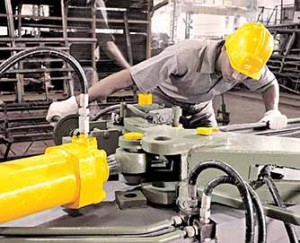
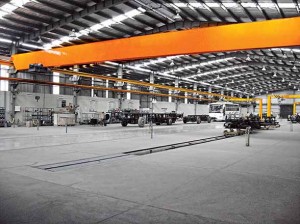
Alternate propulsion mediums
JCBL is working with OEMs for their CNG buses to cater to the North Indian market. OEMs stand to benefit from offering fully-built buses. With the regulation already in place in markets like Delhi NCR, the objective is to make available an alternate fuel product to achieve that extra market reach. “Almost 80 per cent of the market in Delhi-NCR is chassis driven. A fully built CNG bus is seeing demand where there is a tender, says Babbar. Distribution and availability of CNG is an issue, and in many areas , hybrid and electric buses are being looked upon as an alternative. It will be a value game, opines Babbar. He quips, “Depending upon the area of operation, the one that offers better value for money will be the game changer as far as alternate fuel vehicles are concerned.”
After identifying an opportunity, JCBL tied up with bus components manufacturers in Europe. The intention was to control the balance of supply with costs. “We started with seats, then we got into bus components and then FRP components under MSL brand.” says Babbar. To cater to the captive requirements, the company developed in-house FRP shop for its bus body building needs. Though Acrylonitrile Butadiene Styrene material (ABS) is also in the usage based on the customer requirements along with PVC coated sheets and pre-coated sheets, the demand for FRP is rising. JCBL, over the last few years, has been maintaining a CAGR of 20 per cent. It has clocked Rs.125 crore revenue in FY2015-16. Close to 50 per cent of this was generated from OEM business. Close to ten per cent came from defence applications. The rest was generated from private business. “We expect to earn Rs.150 crore in the current financial year,” says Babbar. JCBL is experiencing good demand in school and staff buses. With GST coming in, JCBL expects things to simplify. Hoping to source chassis from a chassis manufacturer directly, JCBL, it is clear, is keen to turn into a bus manufacturer. It is aiming to become a bus manufacturer rather than remain a mere bus body builder. Concludes Babbar, “GST will be beneficial in cutting down time taken to transport. It will simplify and cut down taxes. All this will mean considerable cost savings for us.”