Eicher’s much-awaited foray into the two-to-3.5-tonne SCV segment is driven, incorporating real-world feedback and reverse engineering to meet customer demands at the state-of-the-art manufacturing plant in Bhopal, writes Ashish Bhatia.
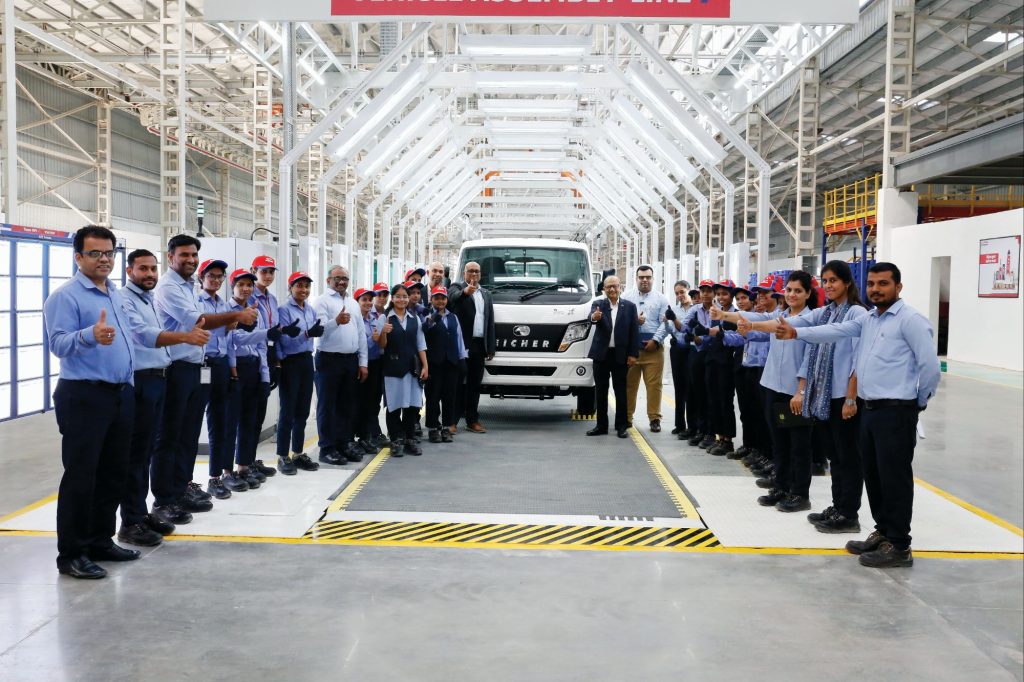
At the VE Commercial Vehicles (VECV) manufacturing plant in Bhopal, there is a calm yet resolute determination among the workforce. Last year, the company ventured into the Small Commercial Vehicle (SCV) segment, which ranges from two to 3.5 tonnes in Gross Vehicle Weight (GVW). This move has inspired VECV to plan its future actions based on the momentum and encouragement received from its customers. Aside from the two-tonne segment, Eicher has established its presence across all tonnage categories, from SCVs to Medium and Heavy Commercial Vehicles (M&HCVs).
CV Magazine was invited for an exclusive preview of the Eicher Pro X series drawing its lineage from the Eicher Pro Series, which is set for commercial rollout in the first quarter of FY25. During a tour of the state-of-the-art manufacturing processes utilised for the SCV, it became clear that the Eicher Pro X is a product of customer-driven development. It incorporates real-world insights to meet contemporary needs and is supported by advanced manufacturing facilities, as noted by Vinod Aggarwal, the Managing Director and CEO of the company.

Aggarwal, Immediate Past President of SIAM and an industry veteran expressed a deep sense of pride in the team’s achievements as they reached critical production milestones ahead of the commercial launch. The plant’s workforce has gained valuable hands-on experience through the production of the Eicher Pro 2000 series, which they have applied to refine processes for the lighter Pro X platform.
Key differentiators contributing to this success story include the use of advanced automation, mechanised transfer facilities, and innovative technology integration in the painting booths. The plant features an impressive cabin holding capacity and a modern assembly line that adheres to Just-In-Time (JIT) principles through a well-organised tier supplier ecosystem. Unlike the traditional parallel approach where complex sub-assemblies are worked on simultaneously with the main assembly line, parts that need to go on the main line are unloaded at dedicated truck bays. From there, the sub-assemblies are fed directly to the main assembly line. This streamlined methodology marks a significant evolution for OEMs, including VECV.

Capacity Augmentation with the SCV foray
The new plant in Bhopal, India, was prepared by VECV for its ambitious commercial rollout. With this facility, VECV achieved an impressive annual production capacity of 140,000 units. As Eicher’s flagship plant, built from the ground up according to Industry 4.0 standards, Aggarwal emphasised that this initiative was significantly different from modernising an existing facility. Construction of the plant commenced during the COVID-19 pandemic in 2020, and work progressed seamlessly, he noted.
The Bhopal plant will focus on Light and Medium Duty (LMD) trucks, alongside the new SCV series. Meanwhile, the Pithampur plant will be dedicated to Heavy Duty Trucks (HDTs), except for a few Medium Commercial Vehicles (MCVs).
New segment alignments for a well-oiled facility
Before the SCV foray with the Eicher Pro X, VECV began production of the Eicher Pro 2000 Series at its Bhopal facility. Aggarwal highlighted the impressive 580m pillar less assembly line, which provides a clear view from the start to the end, covering a distance of half a kilometre. “It’s a great sight and perfect for the new foray,” Aggarwal stated. With the inauguration of a state-of-the-art paint shop and Body-In-White (BIW) line, the assembly line is nearing completion. According to Aggarwal, manufacturing is set to commence in early 2025.
With the driveline at the centre of the vehicle’s design, Aggarwal shifted his focus to highlight the Pro X cab, which has been intentionally developed for enhanced aesthetics, driver comfort, and safety. He noted that new stampings and a new Body-In-White (BIW) line would require significant capital expenditure (CapEx). At the Bhopal facility, 16 robots are utilised for approximately 1,800 welding spots on the Eicher Pro X, addressing challenges associated with human resources. These welding operations employ Mid Frequency Direct Current (MFDC) technology, ensuring that sparks remain contained within a well-defined welding zone. This technology also integrates genealogy or material flow tracking, achieving a new level of transparency in the Eicher Pro X’s journey from raw materials to the finished product delivered to the customer, as part of Industry 4.0. This allows for any faults to be traced back to the supply-side error if necessary, further ensuring that the initial yield is fault-free.
The investment in BIW tooling for the SCV Eicher Pro X line, especially for the externally sourced stampings welded at the plant, amounts to a CapEx of Rs. 200 crore. At the Bhopal facility, there is no in-house storage. Instead, third-party suppliers provide the necessary models on the production line, synchronised through advanced Production Planning and Control (PPC) systems. This process involves efficiently managing resources, schedules, and various aspects of manufacturing. With 100 per cent localisation, except for out sourced chips, the development is fully indigenous, confirmed Aggarwal.
The bare Eicher Pro X is painted to ensure no rust, peel-off, or decolouration for six lakh kilometres and six years in an industry-first initiative. To attain this quality benchmark, the mission is to produce cabins of the highest quality. A dual coating system is observed here with the pre-treatment followed by the base coat and the top coat. The lux level of 95, the highest quality has been attained akin to cars. Set up by Durr of Germany, a global leader in planning and implementation of paint shops has ensured that Eicher offers the best to the Pro X customers. The Bhopal paint booth is a level up from Pithampur, confirmed Aggarwal. The new quality benchmark is expected to further trickle down to other segments of the OEM.
Strategic partners and export aspirations
Aggarwal praised the strategic partners for bringing unparalleled global expertise in processes and technology, which gives Eicher a competitive advantage. “Our partners play a crucial role in driving our vision of modernising commercial transportation in India,” he stated. The paint shop can hold 65,000 cabins, with the potential to scale up to 90,000. It can paint between 1.65 million and 2.3 million cabins, accommodating both Small Commercial Vehicles (SCVs) and Light Medium Duty vehicles (LMDs), which provides Eicher with a high level of flexibility.
Eicher’s export ambitions can be easily met due to the implementation of IoT 4.0 standards. This capability allows Eicher to compete with Japanese trucks in markets like South Africa and Southeast Asia. With UD Trucks, VECV already has experience in producing Japanese technology. The aim is to manufacture vehicles that meet the highest quality standards.
Aggarwal noted that traditional pass throughs are no longer relevant for VECV, as target price positioning is the foundation for all product development and distribution. This approach suggests higher profit margins per vehicle, leading to a more profitable business without compromises. VECV is confident of sustaining this momentum in collaboration with its suppliers.
Eicher Pro X rollout strategy
VECV has accounted for an initial capacity of approximately 40,000 to 50,000 units for the SCV, with scalability options available for future expansion. The vacant spaces along the production line indicate that there is room for growth as needed. With a strategy to launch the Pro X in its Electric Vehicle (EV) version ahead of the Internal Combustion Engine (ICE) options, Aggarwal attributed this approach to VECV’s commitment to sustainable development. “This vehicle is highly relevant to that strategy, as the viability of electric SCVs can be realised more quickly due to the charging infrastructure being focused on localised areas for last-mile delivery,” he explained. Additionally, the battery packs are smaller, which aligns with the shorter distances covered, thereby reducing the upfront costs for operators compared to Heavy Commercial Vehicles (HCVs).
Both the EV and ICE versions of the Pro X will be manufactured on the same assembly line, indicating a high degree of operational flexibility. VECV is firming its presence in the segment ranging from two to 55 tonnes, excluding the nearly two lakh units of Total Industry Volume (TIV) left to be tapped in the sub-two-tonne segment. However, considering Eicher’s careful strategy, a foray into this segment cannot be ruled out. Aggarwal noted that from the announcement in Q4-FY24 to the approaching Q1-FY25 launch, the Pro X has undergone extensive testing, including both virtual simulations and real-world trials for various customer applications at the NATRAX track in Pithampur. He stated that the Pro X has accumulated hundreds of thousands of kilometres during its pilot runs.
Co-development with the customer
The development of a new product emphasises the importance of capturing the customer’s genuine feedback in their native language, according to Aggarwal. He stressed that this feedback must be translated into technical specifications. Understanding unmet customer needs and providing additional value for customer comfort are crucial in this process. In industry terms, this involves using Quality Function Deployment (QFD) and the Six Sigma methodology, which focus on meeting the demands of a broad customer base, ensuring that customer requirements are incorporated into the features of products like the Pro X and its related services.
Aggarwal prefers to be seen as a competing brand, given the company’s excitement about entering a large market as both a pioneer and a challenger in the Small Commercial Vehicle (SCV) segment. The estimated market size for the two-to-3.5-tonne category is approximately 330,000 units and is steadily growing, largely due to a shift from the sub-two-tonne segment to the segment where the Eicher Pro X aims to establish itself. Aggarwal identifies this segment as the “sweet spot,” ideal for city and last-mile transportation. He pointed out that the Eicher Pro X is classified as an SCV pickup, combining the best features of both categories. To succeed in an environment with strong competitors, VECV is focusing on customer service as a way to make its mark.
Skilling and upskilling initiatives
In Bhopal, a new skilling centre is being established, taking inspiration from the successful models in Pithampur and Dewas. Furthermore, employee exchange programs are being implemented to enhance collaboration and learning. Aggarwal emphasised the importance of gender diversity in the workplace and stated that achieving a balanced mix of genders is a key initiative for the organisation.
Eicher and MadhYa Pradesh
Aggarwal took a moment to reflect on Eicher’s partnership with the state of Madhya Pradesh, which began in 1985. VECV is proud of its pioneering efforts in establishing manufacturing plants including Pithampur and Mandideep, where the Eicher Group set up its Eicher Tractor plant. “We have successfully transformed these non-industrial areas into thriving industrial hubs, contributing to the growth of three significant industrial zones in Madhya Pradesh. This region, situated in the heart of India, serves as a hub for the stakeholders of the Eicher Group.”