Covestro is rooting for the penetration of high-tech polymer materials in CVs. Prateek Pardeshi draws attention to the diverse applications of the company’s solutions.
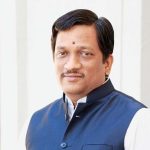
Polymers govern the automotive industry followed by various metals and alloys. Be it the bumper, headlights, mirrors on the exteriors, or the dashboard, instrument clusters in the interiors. Covestro India Pvt. Ltd, (Covestro India) is claimed to lead the space with its range of high-tech polymers. The company offers a wide range of polyurethane and polycarbonate-based raw materials for the CV industry among other industries. Divakar Gokhale, Head of Mobility, Indian Subcontinent at Covestro India Pvt. Ltd. in an exclusive conversation mentioned, “As the classic automotive industry develops further it will define the future needs of such material technologies for such special applications.” “Our experts in this product stream are always willing to get into a discussion with the industry players,” he stated.
Interior applications
Covestro India co-develops the solution with the OEMs or ODM depending on their wish list and concepts. They provide tailor-made solutions coming from its broad product portfolio of Polycarbonate (PC) and PC blends, together with speciality films and coatings that allow for diverse applications. Every innovation comes with a huge R&D cost but needs to be offered at an affordable price, quipped Gokhale. He explained, how with the premium experience, multi- functionality, and efficiency improvement that the company brings to the table, the lowered costs are directly linked to the input materials. Covestro India is also linked across the value chain with some cutting-edge technology providers who can help bring many new ideas to life for its customers.
Makrolon® PC and Makrofol® films are used in touch-panel technology, for example. The application necessitates high purity, clarity, dimensional stability, scratch resistance, and a few other features. Such applications for CV interiors are easily possible with electronic integration. Digitalisation has taken over analogue systems for over a decade now. Infotainment systems are a testimony to this evolution. The erstwhile transistor units have made room for sophisticated aircraft like cockpits with dials and levers giving way to new alternatives. Notably, these displays are made of polycarbonate where Covestro AG excels. At the right price points, the opportunity to tap the CV segment is huge.
On the Dashboard
A dashboard, which hosts a couple of things like the Infotainment system, AC vents, cluster meter, are generally made up of foam and PolyVinyl Chloride (PVC). OEMs and tier1 suppliers are turning innovative in their concepts and designs. They are offering a spectrum of features across the board to cater to different CV segments. “At Covestro India, we demonstrated innovation by utilising our unique Makroblend® product for backlight applications utilising natural materials such as leather, wood, and stone. The dashboard design has changed substantially as a result of the emobility and autonomous vehicle trends,” explained Gokhale. He drew attention to leading international OEMs incorporating long/large displays, and signalling change by futuristic shifts from old analogue metres to digital metres. Also, OEMs are now replacing conventional ORVMs with screens and cameras. All of this has resulted in changes to the dashboard’s design and appearance, he opined.
The next generation of CVs are beginning to draw parallels with passenger vehicles. Recent launches are testimony to soft-touch buttons making inroads into the dash and onto the steering wheel. This comes as a shift from the erstwhile use of thermoplastic polyurethane. When tailored for injection moulding Desmopan® Thermoplastic PolyUrethane (TPU) grades offer a fast development cycle, high mechanical values and advanced processing. Desmopan TPU has a very soft feel as well as good abrasion resistance according to Gokhale. No additional coating is required. Makrofol® PC films are used for haptic touch applications. These can be back-lit, opaque/translucent coloured, and have a matt or gloss finish, depending on the design. A coating process can also be used to achieve a soft touch.
Exterior applications
Indians are obsessed with a chrome finish which is synonymous with premium in this market. Especially on headlamps, brake lights, weather trims etc. Covestro India offers special Bayblend® grades. The BayblendT45PG for such chrome finish applications is deemed apt. Covestro has also developed a 2k/3k moulding with an In-Mould Decoration (IMD) for premium applications and some sensor-based functionality integration. Headlights and tail lights made of glass previously are also known to have shifted to polycarbonate. The latter was known to turn yellow after long usage, however, the specially developed Makrolon® AL grades for head-lamp lenses give long-lasting performance together with lightweight. The Covestro Bayflex® for example is used to manufacture OEM applications (factory fitted) on passing the mandatory international safety standards. Only after the required test and qualifications, these are commercially rolled out.
Other than that, AMECA approvals in lighting applications for the exports market and ARAI approval for India are necessary for new vehicles/vehicle systems. A few decades ago, the automotive industry replaced metallic bumpers with ThermoPlastic Olefin elastomers (TPO). This was done keeping pedestrian safety in mind in the year 2017 since TPO is made up of softer materials. The Government of India banned any kind of metal crash guard or bull bar on vehicles and made fibre bumpers a mandate. Similarly, other automotive ancillaries such as reinforced chassis etc. are other examples moving towards the use of alternative materials.
Covestro has had a good second quarter (Q2FY2022). In the first nine months of 2021, APAC sales accounted for Euro 1700 mn in a growth of 61.3 per cent over the same period last year as per the company’s Q32021 statement. At an investor conference in 2021, the company hinted at planning an investment of Euro one billion on circular economy projects over a 10-year timeline. CVs are expected to contribute to the revenues significantly, concluded Gokhale. The new Group structure that is known to have come into effect since July 01, 2021, has reorganised the organisation with Polyurethanes, Polycarbonates, and Coatings, Adhesives specialities formed as new entities. The objective is to cater to specific customer needs and markets with an eye on both profitability and sustainability. Notably, the 15.4 per cent growth in PolyCarbonates, in Q2FY22 over the same period last year is attributed to the overall growth in the automotive and transportation industry signalling a sign of things to come from the global parent and its Indian arm.
Also read, The future of the Indian CV industry